Incident Investigations
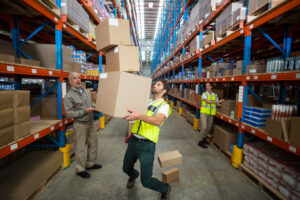
WHAT’S AT STAKE?
Industrial incidents occur every day. Some are major, with injuries to workers as well as damage to property, but most are minor and do not involve time lost, medical care or repairs to property. Incidents can be controlled and prevented. One of the best ways to prevent incidents is to investigate the causes of each incident that occurs. The degree of investigation depends on the potential severity of the incident.
The term incident is used in some situations and jurisdictions to cover both an “accident” and “incident”. It is argued that the word “accident” implies that the event was related to fate or chance. When the root cause is determined, it is usually found that many events were predictable and could have been prevented if the right actions were taken – making the event not one of fate or chance (thus, the word incident is used).
WHAT’S THE DANGER?
When an incident happens in the workplace, everyone will be busy dealing with the emergency. Helping injured victims, assessing if the danger has abated, trying to piece together what happened. So, it’s critical to be prepared to investigate an incident before one occurs.
All incidents – regardless of size or impact – need to be investigated, including near misses. The time spent, and the detail involved will vary depending on how complex the incident is.
To prevent incidents from occurring is the obvious goal. Employers and businesses want to avoid all the problems and costs of unwanted incidents.
There are a myriad of costs resulting from business interruption, emergency response and clean-up, increased regulation, audits, inspections, and OSHA or EPA fines. Regulatory fines can become costly, but litigation costs can often substantially exceed OSHA and EPA fines. Employers may find that they are spending money to correct immediate causes of incidents that could have been prevented, or reduced in severity or frequency, by identifying and correcting the underlying system management failure.
HOW TO PROTECT YOURSELF
Once the incident has happened the swing to an investigation must commerce immediately. We are now in the investigation phrase. The first step is the following a WRITTEN PLAN.
WRITTEN PLAN
- How and when management is to be notified of the incident.
- Notifying safety regulators according to incident reporting requirements.
For example:
- All work‐related fatalities within 8 hours.
- All work‐related inpatient hospitalizations, all amputations, and all losses of an eye within 24 hours.
- Who is authorized to notify outside agencies (i.e., fire, police, etc.)?
- Who will conduct investigations and what training they should have received?
- Timetables for completing the investigation and developing/implementing recommendations.
- Who will receive investigation recommendations?
- Who will be responsible for implementing corrective actions?
ESTABLISH THE INVESTIGATIVE TEAM
The most effective investigations are conducted by a Team in which managers and employees work together each bringing in a different perspective, understanding and knowledge. Working together will also encourage all parties to “own” the conclusions and recommendations and to jointly ensure corrective actions are executed in a timely manner.
INVESTIGATIVE PROCEDURE
A systematic approach in investigating all incidents to find the “Root Causes”.
1. Preserve and Document the Scene
The first step in the investigation is to secure the incident site to prevent evidence from being moved, altered, or tampered with.
- If evidence goes missing or is messed with – you are going to miss out on important clues on what caused the event.
- Use cones, tape, or barriers to physically block off the scene.
- You can use photos or videos to preserve and document the scene.
Document the incident facts:
- Date and time of incident
- Investigator
- Name/s of the injured
- Injury description
- Date, time, and location of incident
2. Collect Information
Collect information leading up to the incident, the incident itself, and other important information is necessary to establish a timeline, identify victims and witnesses, and begin to uncover the initial and root causes of the incident.
Interview witnesses and the victim/s. The sooner a witness or victim is interviewed, the more accurate and candid his/her statement will be.
Set the interviewee at ease:
- Clearly state the purpose of the investigation and interview – to learn how to prevent future incidents and notto blame any one person.
- Interview witnesses separately. A witness might say more if they aren’t in the same room as their supervisor, co-worker, or the victim. The same is true for when you interview the victim.
- Let employee know they have a right to have employee representative (e.g., labor representative) present, if available/appropriate.
- Conduct interviews in a quiet space, although in some cases, it might make sense to interview someone at the scene of the incident. It might help them explain something better, jog their memory, or help you both put questions and responses in context.
The interview:
- Ask the individual to recount their version of what happened and don’t interrupt them.
- Take notes and/or record the responses; interviewee must give permission prior to being recorded.
- Have paper and pen/pencil available for interviewee.
- Ask clarifying questions to fill in missing information; repeat back to the interviewees the information obtained; and correct any inconsistencies.
- Ask the individual what they think could have prevented the incident.
In addition to interviews, other sources of helpful information include:
- Equipment manuals
- Industry guidance documents
- Company policies and records
- Maintenance schedules, records and logs
- Training records (including communication to employees)
- Audit and follow‐up reports
- Enforcement policies and records
- Previous corrective action recommendations
3. Determine the Root Causes.
The root causes are the underlying reasons why the incident occurred. Root causes generally reflect management, design, planning, organizational and/or operational failings (e.g., employees were not trained adequately; a damaged guard had not been repaired).
If you truly want to prevent a repeat of an incident, you must go beyond the easy surface causes – “worker was careless” or “employee didn’t follow the SOP.” Focusing on the easy causes is a lazy way out and it won’t get you the answers you need to put meaningful corrective actions in place.
Remember: Investigations are not effective if they are focused on finding who to blame because they will stop at the initial incident and stop short of discovering the root causes.
4. Implement Corrective Actions
Your investigation isn’t done until all the underlying causes of the incident have been identified and corrective actions are in place.
Some of the corrective actions will be quick and easy fixes; others may take more time and planning. Some may be specific and address a root cause directly and others may be sweeping improvements to the safety program in general.
Regardless, it is important that you communicate the corrective actions throughout the workplace. Employees pay attention to what management pays attention to and what management ignores. If you ignore incidents or don’t follow through on corrective actions your employees will get the message loud and clear. Employee safety isn’t valued.
Take time to develop appropriate corrective actions and manage them through to completion.
FINAL WORD
Investigations are not effective if their focus is to play the “blame game.” The focus should be discovering the root causes of the incident.