ESSENTIAL 29: Machine Guarding
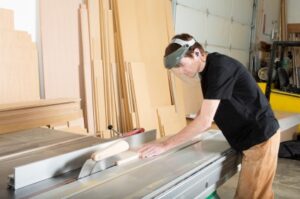
Key Takeaways:
- Understanding the hazards of working with mechanical equipment, including where those hazards occur and the motions and actions that cause the hazards
- Recognizing the purpose of machine safeguarding, safeguarding device requirements, factors that influence safeguarding methods, and the safeguarding methods used to protect you from mechanical hazards
- Acknowledging your responsibilities to utilize machine safeguards properly
Course Description
Any machine that is not properly safeguarded can cause serious injury, such as crushed or severed fingers, hands and arms, eye injuries, and even blindness.
If you have seen the gruesome result of a complex machinery accident, then you will appreciate the machine safeguards. Safeguards are the simple devices or methods that protect and make it difficult for workers to injure themselves while working on a machine. They may come in the forms of a shield or guard to protect from sparks, or a grate that keeps them away from the churning part of a rotary blade.
Taking shortcuts around machine safety protocols are a frequently cited cause for many machine related accidents, happening when workers decide to forego the normal protocol of working with a safeguard and bypass it altogether, leaving them with considerable risk of harm and injury. You must never ignore the engineered controls or safety features of machinery, they exist for a reason.
OSHA standards require that one or more methods of machine guarding be provided to protect the operator and other employees in the machine area from hazards created by moving parts, in addition to preventing contact with other hazards such as heat, non-ionizing radiation, sharp edges, etc. As well, safeguards need to be secured in place, protect against falling objects, create no new hazards or interference, and allow for safe maintenance and lubrication of the machinery. Poor and inadequate maintenance of machinery is a situation commonly related to machine accidents, so awareness in those situations is critical to personal safety, as is recognition of safeguards and proper protocol, like shutting down equipment, and locking out operation.
A safeguard by definition will need to prevent hands, arms, and any other part of a worker’s body from making contact with dangerous moving parts. Fantastic safeguarding systems physically eradicate the potential of the operator or another worker placing parts of their bodies near hazardous moving parts. Often, physical barriers are an effective means for providing this protection, but sometimes this is not possible depending on a machine’s point of operation. In such events, a presence-sensing device is used, which stops a hazardous action before contact can be made.
Other times, restraints such as a sweep or pull-back device are used. These devices require physically removing the operator’s hands from the point of operation. Another way to keep an operator’s hands away from the point of operation hazard are two-hand constant pressure operating switches, which must be held down in order for the machine to operate. Many machines use combinations of both types of protective devices. Lastly, when hazards are not within 7 feet of a place where they are accessible, they are considered guarded by location.
How are safeguards decided to be necessary for a piece of machinery? The type of operation, the size and shape of material, and the method of handling, placing, and removal of the material at the point of operation are all considerations made by a safety professional. As well, considerations may also involve the physical layout of the work area and the production requirements. To decide the correct safeguards, there needs to be both a detailed understanding of the machinery and of the procedure for operation that workers must follow to accomplish their job.
Machine Safeguarding Methods
- Barrier guards
- Presence-sensing and/or physical restraint devices
- Guarding by location/distance
- Feeding and ejection methods
Miscellaneous aids
The first method of protection is barriers protecting against hazards from all sources, including access prevention to danger areas. This area, sometimes called the danger zone, is where the machine works, where the operator must stay clear during the machine’s operation cycle to prevent injury. In general, there are four types of barrier guards: fixed, interlocked, adjustable, and self-adjusting.
The next method for machine safeguarding is safety devices. A safety device could do various things and for example, it may occupy both of the operator’s hands to keep them from entering the danger zone while the machine is cycling. This type of device will force the operator to keep both hands and their body out of danger. Alternatively, the safety device could also be a presence-sensing kind that detects the presence of anything entering the danger zone and stops the machine in mid-cycle. A different form of device is a physical restraint, which is designed to physically withdraw the operator’s hands from the danger area during operation.
The third way to safeguard is through location or distance. Using distance means that hazardous moving machine parts must be inaccessible or far enough away to not present a hazard to a worker during the normal operation of the machine.
Lastly, miscellaneous aids are the another method of machine safeguarding. Although miscellaneous aids do not completely protect against machine hazards, they can provide the operator with an extra margin of safety. Awareness barriers, shields, placement and holding tools, and push sticks or blocks are all examples of this type.